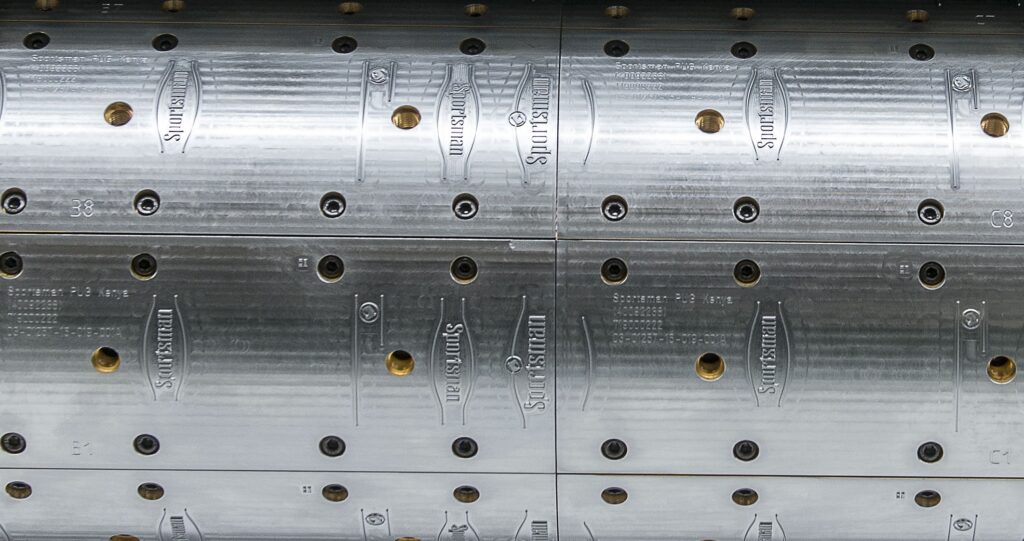
Case
Printpak
A unique solution at the boundaries of technical feasibility for printpak
Over 10,000 kilometers away from Madern’s headquarters, in Nairobi, Kenya, you will find the premises of Printpak, a manufacturer of various types of packaging. Despite the long distance between the two company premises, the collaboration between Madern and Printpak is pretty good. “There is always someone available whenever I have a question or need a solution to a problem,” says Printpak operations director Shiv Savani.
Printpak, a Madern International customer for over 10 years, uses the cutting, creasing and embossing tools Madern supplies. Recently, the company asked for help in modifying the cylinder sets for new cigarette pack designs, allowing Printpak to further control costs.
Contact Madern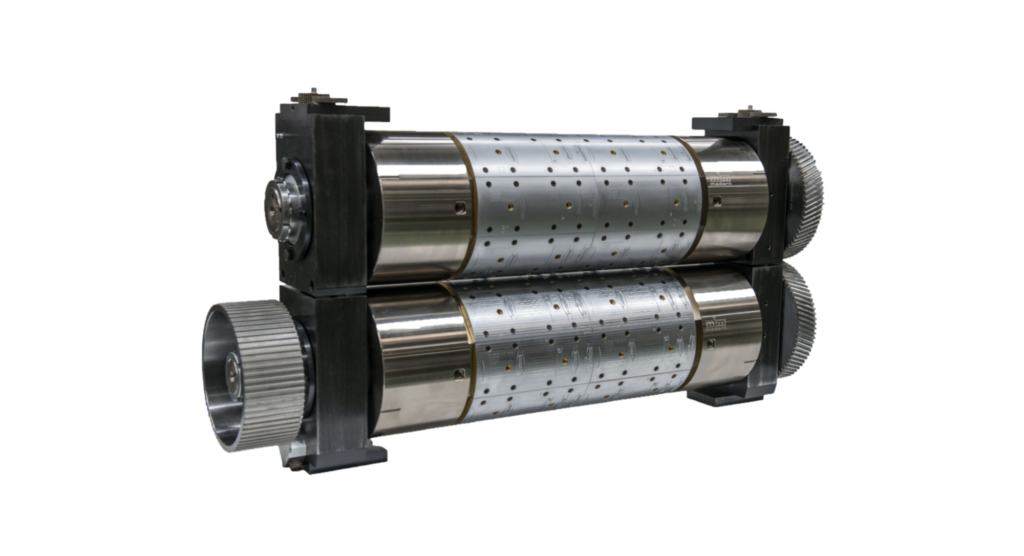
"I am grateful to madern for providing me with a workable solution to this difficult challenge. together, we have achieved a splendid final result."
Solution for investment costs
Each day, various packaging materials such as rubber, plastic and cardboard enter Printpak’s factory and leave the premises later as complete packaging materials. Among the packaging manufactured by Printpak are various types of cigarette packs. A challenge for Printpak was the fact that no two pack designs are the same. “Here, the dimensions of cigarette packs are the same, but the design and embossing vary with each type,” explains Mr. Savani. “Because we had to order new cylinders for the production machine and so-called modification parts for each new embossing design, the investment became too costly. We asked Madern to come up with a solution for the flexible production of the various cigarette pack designs without having to invest in new cylinders and parts each time.”
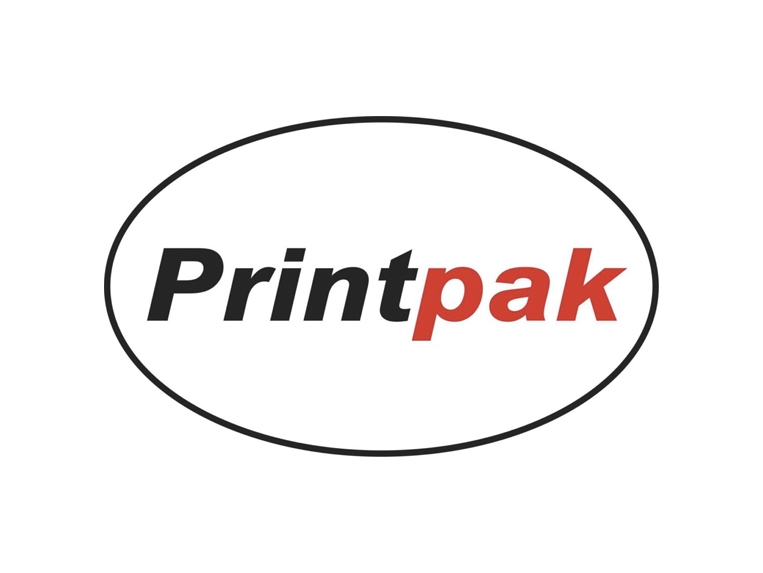
Easily interchangeable cylinder segments
Printpak’s request presented Madern with quite the challenge. In general, complete cylinders are supplied based on the design of the packaging. This means that when a new design is launched onto the market, a new cylinder must also be made. But this is exactly the situation Printpak wants to get rid of. Madern’s engineers explored the boundaries of technical possibilities in order to meet Printpak’s requirements. Eventually, the idea arose that when changing the packaging design, instead of remanufacturing the complete cylinder sets, we would create a cylinder set with easily interchangeable segments. This way, Printpak can switch the segments when their customer wants to apply a different embossing design. They no longer need to buy a new cylinder set.
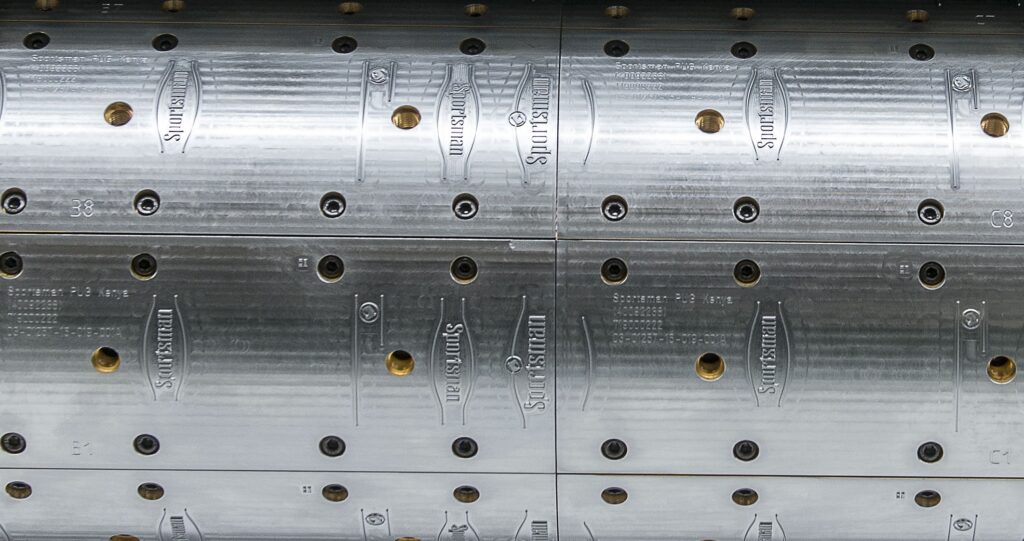
Tailor-made solution
This solution with easily interchangeable cylinder segments reduces investment costs, but posed another challenge. Savani: “In order to minimize production downtime between cylinder segment changes, it had to be possible to change the high-precision segments in the shortest possible time. The embossing patterns also had to fit on these segments, of course, and the purchase price could not be too high.” Based on these additional requirements, Madern designed various sets of segments for the cylinder sets. After a successful trial period, Printpak is now using the segments with great satisfaction.
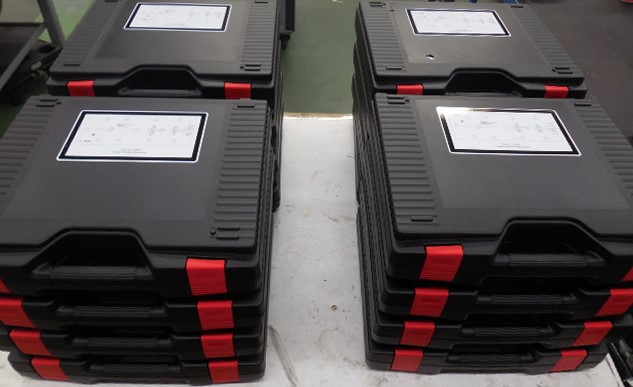
High quality embossing
“The segments work well and the embossing is of excellent quality,” says Savani. “Switching segments is fast and effective because Madern took this into account in the design process. We would have missed out on many contracts if we had not been able to reduce costs while remaining flexible with new designs for the packs to be manufactured. I am glad that there is always someone at Madern who thinks along with me, even if something seems impossible at first. I am grateful to Madern for providing me with a workable solution to this difficult challenge. Together, we have achieved a splendid final result.”
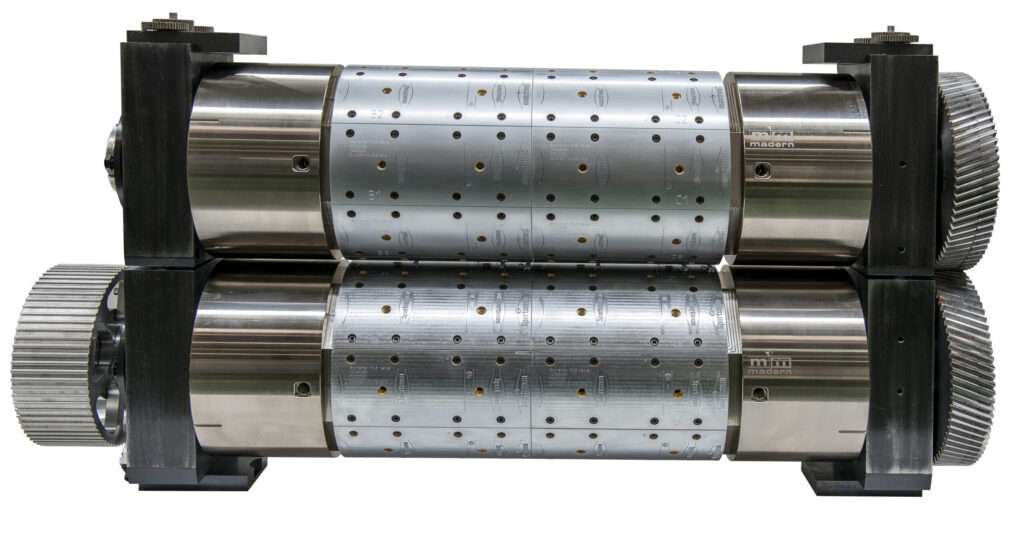