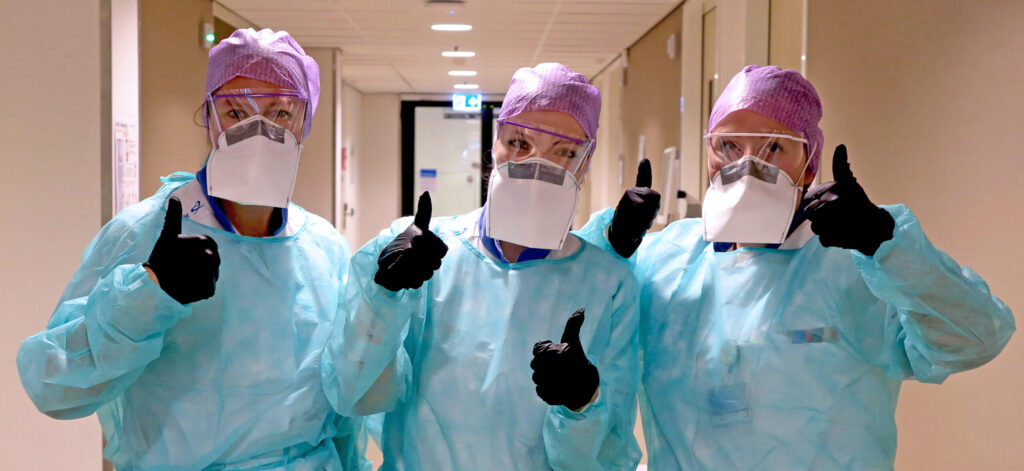
Case
Madern achieves the impossible in mass production of medical mouth masks
Due to coronavirus there was a need for more medical mouth masks
With the coronavirus outbreak in the Netherlands, healthcare was faced with a major challenge. Hospitals suddenly needed sufficient medical mouth masks to protect their staff responsible for the care of the seriously ill Covid-19 patients. Madern helped Reinier de Graaf Gasthuis in Delft to manufacture a machine that automatically cuts mouth masks from protective fabric at high speed.
With the increase in hospitalization of Covid-19 patients, the use of medical masks at Reinier de Graaf Gasthuis also increased significantly. At the height of the first corona wave, it turned out that there was only a three-day supply of mouth masks. At that time, hospital management ordered the in-house manufacture of mouth masks.
Contact Madern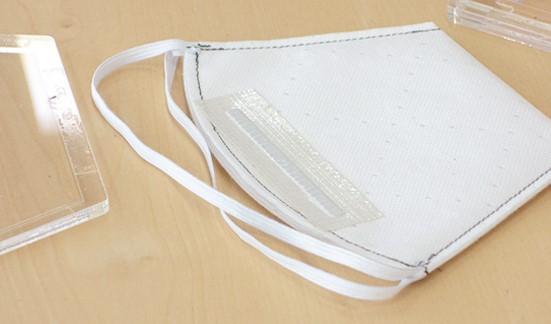
Cohesion and solidarity
During the first wave of the coronavirus, Madern’s orders declined as customers postponed projects. In the spirit of cohesion and solidarity, the company wanted to do something for the sector that was most affected by the virus at the time. When Madern heard the news of the efforts of Reinier de Graaf Gasthuis to make its own mouth masks, it saw an opportunity to lend a helping hand. The company voluntarily converted an old roller into a roller that automatically die-cuts (punches) mouth masks from the polypropylene fabric from which the mouth masks are made. “This is a lot quicker and easier than the way the mouth masks were die-cut in the first week,” says Van Olphen. “The machine provided us with mouth masks faster en more efficiently.” In cooperation with another party, post-processing, such as attaching the rubber bands, was also automated.
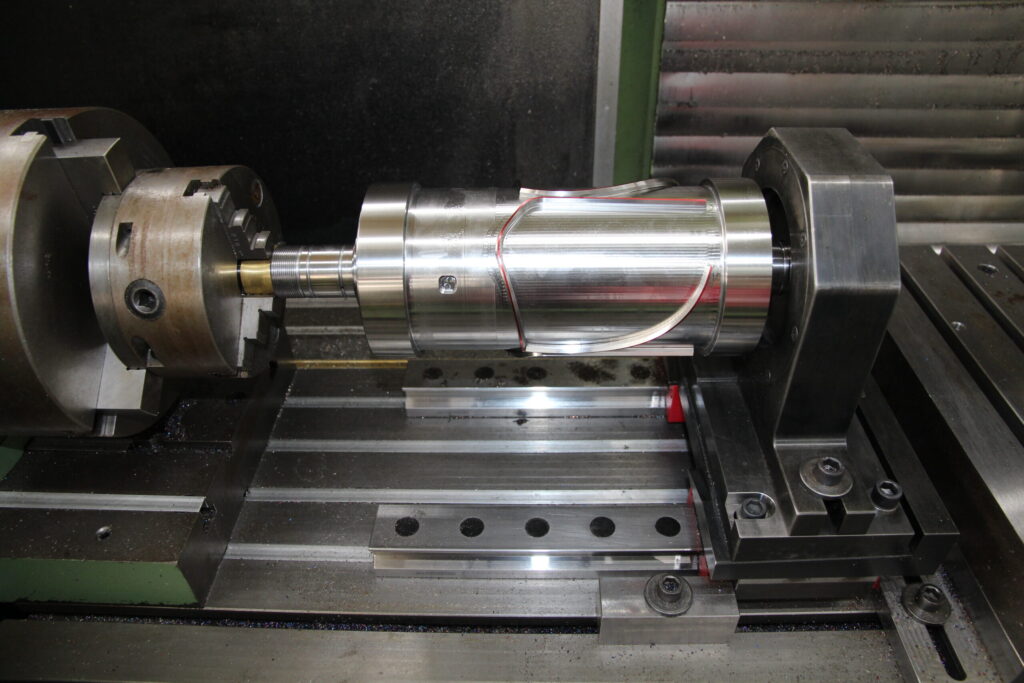
Adaptability was vital
When Madern started making the die-cutting machine for mouth masks, the company had to adapt quickly because time was of the essence in setting up a production line. Therefore, the company had a lot of contact with local companies, which helped in the realization of the die-cutting machine. It was additionally challenging that Madern employees suddenly had to make a machine for die-cutting fabric, while they are used to making machines for cutting and processing cardboard. The company also had to find out how safe and practical the mouth masks, which the machine cuts, were when used. When the first roller came to the end of its life cycle, Madern delivered a new one at cost price. Jean Madern, Madern’s Managing Director, is pleased to have been able to contribute to the realization of the in-house production line of Reinier de Graaf Gasthuis. “We are proud of the fact that we were able to set up a production line this quickly, which still provides new medical mouth masks for the hospital staff every day. It feels good that our efforts have helped the health care workers do their jobs safely.”
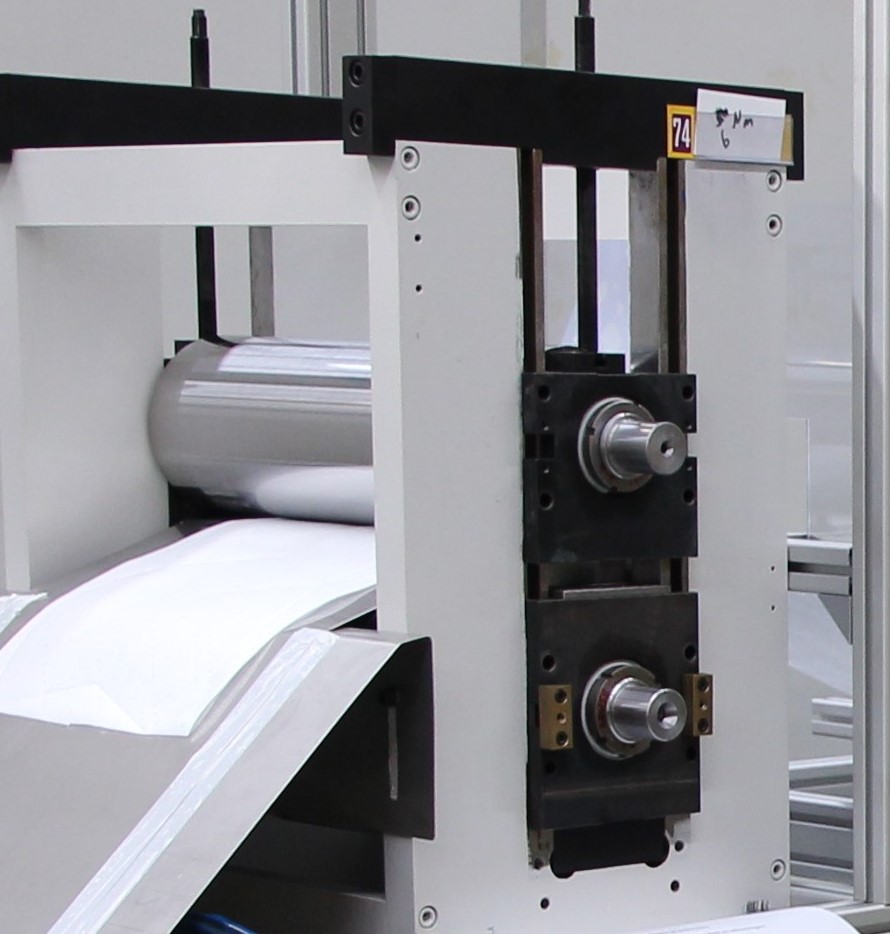
All on a voluntary basis
Madern and the other parties that helped out made all their efforts on a voluntary basis. “It’s an extraordinary story,” says Van Olphen. “Beforehand, you think that producing so many medical mouth masks yourself is impossible, but thanks to the efforts of all those involved, it was made possible. At first, I also thought that these efforts would only be temporary, but in the meantime, we are still making our own masks with the machines and materials that Madern and the other parties voluntarily make available to us. We’re six months in and we have already made 100,000 mouth masks; that is a unique feat. There is a very good organization of logistics and materials behind it. Madern spent a lot of time at the beginning of the project brainstorming and thinking about the creation process, at times even at odd hours. They were being very flexible during those tumultuous times. We are very grateful to them for that. With the selfless commitment of all the parties involved, we achieved the impossible. It is a great success, allowing medical staff caring for patients to do their jobs safely.”
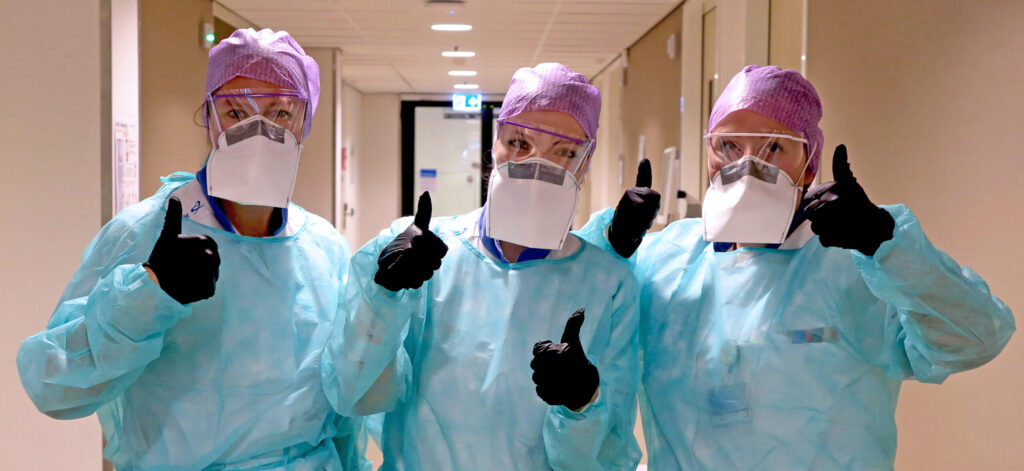
Everything gained momentum
“There was a lot of time pressure,” says Monique van Olphen, who was responsible for setting up the production line as Lean Manager at Reinier de Graaf Gasthuis. “On Wednesday, I was asked to set up an in-house production line and on Saturday, the first mouth masks were already being produced. A couple of sewing workshops, volunteers and fabric providers offered their help and within a few days, the parties produced a prototype mouth mask, which passed the test for FFP-2 mouth masks.” Madern then used a die-cutting machine which highly accelerated the manufacturing capacity of the mouth masks for Reinier de Graaf Gasthuis. Monique: “In the first week, the sewing workshops and volunteers took care of the production of the mouth masks, but producing a large quantity of mouth masks in a short period of time requires a lot of people. A week after we started our own production line, Madern came to us with the proposal to manufacture a machine that would cut the mouth masks out of the material. The machine that Madern made for us enabled us to manufacture a lot of masks each day.”
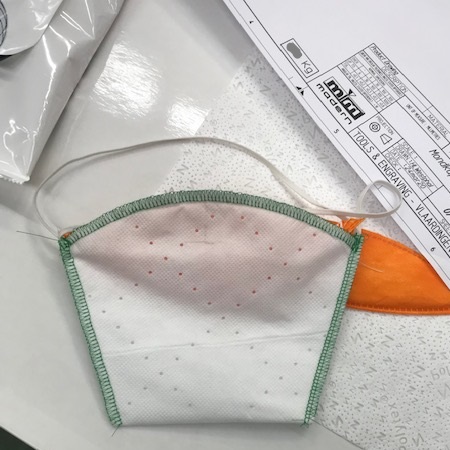